- Diamond wheels&
CBN wheels - For Surface & Cylindrical
- For Profile grinding
- For Internal grinding
- For Tool grinding
- For Sawing & Cutting
- Diamond &
CBN Electroplated tools - Mounted wheels for internal
- Files and wheels
- Diamond &
CBN Compact tools - PCD tools
- PCBN tools
- Wear resistant parts
- Natural Dia. Cut. tools
- Diamond dressers
- Diamond hand-stones
- Other products
- Inquire
- Click Here
- Call us
- +81-3-3759-7405
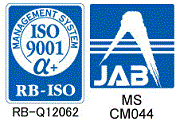
HOME > Diamond &CBN Electroplated tools > Diamond &CBN Electroplated tools
Diamond &CBN Electroplated tools
While Diamond and CBN wheels have an abrasive layer on its periphery which were sintered together with bond and abrasives, there are another type of tools that is electroplated tools which diamond and CBN powder are adhered strongly on the substrates by the unique electroplating method that Cryston's R & D staff developed. Compared with the conventional electroplating, our electroplated tools show remarkable performance with much longer life.
Distinguishing feature of Cryston's Electroplated Tools
- Improved Efficiency
As the tools have diamond or CBN abrasives which have sharp cutting edges retained firmly and uniformly in high density on the core steel, they are well made as tools and when used, they touch workpieces smoothly and show twice better performance than the conventional ones. - Cost Saving
They are easy to handle and very practical for manufacturing goods at small quantity of numerous kinds. They have longer tool life so they save production cost at great deal economically. - Labour Saving
Compared with metal bonded or resin bonded wheels, price is cheaper, and complicated forms can be made. While wear resistance and deformation are not generated so easily, for form grinding it shows excellent performance, and some process in forming are eliminated.
Application of Electroplated tools and workpieces(◆Diamond ◆CBN )
- ◆◆Generally all internal grinding
- ◆◆Edge preparation, and radius grinding of forming tools
- ◆General grinding of tungsten carbide tools
- ◆Truing of grinding wheels
- ◆Machining magnetic materials (such as ferrite), and electronics materials (such as silicon) .
- ◆High precision drilling of thermosetting resin and FRP.
- ◆Machining ceramics and porcelain.
- ◆Sawing and drilling of firebricks, asbestos, tile.
- ◆Fabricating precious stones, jewel, shell.
- ◆Processing tungsten carbide dies before lapping
- ◆Drilling glass, lens centering, bevel edging.
- ◆Combination grinding of tungsten carbide and steel.
- ◆Machining variou hardened steels, and removing distorted part of hardend mould.
- ◆Machining high speed steel, alloy tool steel, steinless steel.
(There are various workpieces other than the above which can be machined. )
Selection of grit size
- Roughing rougher than #120
- Medium grinding #140 ~#200
- Finishing finer than #230
- In general, electroplated wheels are, compared with metal bonded and resin bonded wheels, no. of cutting edges
are more, so in comparison with the same grit size, surface finish achieved by the electroplated tools are slighly rougher.
Please select the grit size to meet your work, along the above as yardstick.
Peripheral speed of electroplated tools
The peripheral speed of electroplated tools differs in workpieces and machining conditions and effects on grinding efficiency at great deal. Adequate wheel speed cannot be set easily but please consider below-mentioned speed as yardstick for your selection.
[Wheel] | |
---|---|
Tungsten carbide | 1000 ~ 1500 (m/min) |
Glass | 1500 ~ 1600 |
Ferrite | 1500 ~ 1800 |
Shell | 1500 ~ 2000 |
Hard rubber | 3000 ~ 4000 |
F R P | 4000 ~ 5000 |
[Internal wheel] | |
Tungsten carbide | 100 ~ 1300 (以上) |
Hardened steel | 100 ~ 1300 (以上) |
[Cutting wheel] | |
Tungsten carbide in green state | 1000 ~ 2000 |
F R P | 2000 ~ 2500 |
Shell | 2000 ~ 2500 |
[Core drill] | |
Glass | 100 ~ 150 |
Shell | 100 ~ 400 |
Suggestion of handling Electroplated tools.
- Since the tools have extremely good ability to grind, slight grinding is required. If the grinding pressure is more than it is required, the tool life will be shortened.
- While dry grinding is possible, wet grinding will improve cutting quality and life.
- Dressing is not particularly needed, but when the abrasive face is loaded or closed, wash or dress the face with brush or GC stick.
- Please do not bend or deform the tool when you use.
- While optimum wheel peripheral speed differs in workpiece and grinding condition, in general, the speed ranges from1,000~2,000m/min.(In case of a small mounted wheel, below 1,000m/min is normally applied.)
- To avoid vibration, please set the tool free from vibration. Run out of the tool effects on precision level achieved and tool life.(In general, wheel run out should be kept below 0.02mm.)
- The mounted wheels may generate severe vertical vibration due to combination of rotation no., protruding size, and run-out and may be bended or broken. To avoid danger, before using the tool
- check out whether dirt and dust on chuck was removed,
- whether the protruding size is kept as small as possible,
- and whether vibration at mounting was set below 0.02mm.